Interview for Automa magazine
Rapid onset of automation and digitalization. Manufacturing companies are going through rapid changes in the current economic growth and, especially in the area of automation, they need solid partners they can rely on. One of the well-proven in practice is the renowned DREAMland company, which is located in the very heart of the Czech automotive industry, in Kosmonosy near Mladá Boleslav, where it provides sales, service and storage of parts for industrial automation, single-purpose machines and robotics . In the last few years, the company has undergone a lot of development and has a lot of plans for this year as well. In an interview for Automa magazine, DREAMland company manager Ing. reveals more about this. František Kysela.
Like the entire industry, DREAMland is constantly developing. How have you grown since our last interview, which was published in 2015?
In less than four years, the number of countries in the world we ship to has increased from 65 to 86. We are significantly have increased the number of items we have in stock for customers from the previous 35 thousand to the current 65 thousand. Hand in hand with our development, the number of employees is growing, currently 44 people work for us. We have sales representatives in the Czech Republic and Slovakia who deal directly with end customers in the automation segment. We have recently added a team of sales representatives who focus on the field of robotics, as we have started to distribute and install Universal Robots and MiR robots, including accessories. , let's stay with automation, which still represents the main part of your activity...
Our main activity really remains the sale of new and remanufactured Siemens parts and a whole range of other manufacturers and brands for industrial automation . Although several companies sell new modules in the Czech Republic, we can also offer a wide range of high-quality refurbished parts or their own repair. Few people offer this on our market to such an extent. Our advantage is a large warehouse, which, although expensive, is highly valued by customers. Thanks to our extensive warehouse of new and refurbished parts, we can deliver the required modules to our customers in a record-breaking time and 24 hours a day.
Do you plan to expand these storage areas further?
Unlike our competition, the customer usually does not have to wait for deliveries from abroad thanks to the warehouse. This significantly shortens delivery times. Of course, it is not even within our power to have all new and refurbished parts in stock, as there would be hundreds of thousands of items. We therefore focus on the most requested of them, which we evaluate through our system.
Due to the effort to offer the widest possible assortment in stock and due to the needs of our service, we have decided to expand these spaces. At the same time, we will also significantly increase the area of our service from the current 100 to 550 square meters. We are finalizing the necessary documentation for this and we will start the relevant construction work this year. We would like to start using the new premises in 2020. We promise to include more repair work and thus become more independent and faster for our clients. The acquired space will also allow us to install other test benches important for verifying the functionality and reliability of the parts we repair. Thanks to this, we will also be prepared for the situation if we have the opportunity to purchase a larger number of machines or parts intended for overhaul, for example from a discontinued assembly line.
In the current economic climate, they are successful and have money. Is there interest in refurbished parts even at this time?
Many of the older parts are no longer made by manufacturers or are available at many times higher prices, and customers have no other option but to look for refurbished ones or order their repair. And this is one of the reasons why we offer a service where we buy older equipment from companies that would otherwise end up in waste when changing their production line. We are also able to buy entire lines, dismantle parts and thoroughly and qualitatively refurbish them. The company that gets rid of the line will make a profit and save recycling costs. Among other things, it is a fundamental contribution from our side to the protection of the environment. It is true that in the Czech Republic, companies often replace the original equipment with a new one when replacing entire lines, but customers further east of the Czech Republic often still use refurbished machines. They therefore need someone who can supply them with the necessary part that is no longer produced. And then there is another point of view: refurbished modules compared to new ones mean great financial savings for our customers while maintaining quality and reliability.
How important is the work of your experts in service?
Here at Kosmonos, we have experts who know how to repair the most requested parts efficiently and quickly. When a customer comes to us with a defective piece, we are able to repair it within a few days. This is significantly faster than the sometimes months-long delivery times of new or refurbished parts requested from suppliers. The ideal situation is when, in the event of a failure of an automation module, we can immediately supply the customer with a new one, whether new or refurbished, from our warehouse, and then efficiently repair the broken one.
Also you have started offering some news in the service. What is it about?
For the most frequently repaired parts, we had new plastic parts made. Thanks to this, we can offer not only the restoration of the functionality of the given module, but also the restoration of the case or cabinet in which it is stored, and other parts. The refurbished part is then reliably functional and at the same time visually almost like new. This is also important for customers today.
Acquisitions in the area of production and supply of single-purpose machines are a significant novelty for you. Did you buy the Montana company from Mladá Boleslav, how is it beneficial to you?
As for single-purpose machines, DREAMland mainly deals with the production of control switchboards and devices according to customer requirements, which we can also program and revive. We are now moving more of this activity to the halls of the Montana company, which we bought in the spring of 2016. It is engaged in the production and assembly of machines, equipment and entire lines for production enterprises, including robotization. It is advantageous to prepare the control components together with the production of these machines. In addition, Montana offers other activities such as industrial automation, metalwork, metalworking, painting, manufacturing of single-purpose machines, manipulators and switchboards. Thanks to this acquisition, we are completely self-sufficient and ready to supply a complete turnkey production or assembly line. We bought Montana after several years of cooperation with the original owner. It is a company with a 25-year tradition, which we are now trying to develop further. We have about 80 other employees there.
In addition, last spring we bought the company Ferrotherm, which deals with programming of control systems and robots, automation technology and production of single-purpose machines. At the same time, it is a distributor of Apex brand tightening tools. And that's not all, you've also started distributing robots. Robotization is a trend in current industry. Are you doing well in this direction?
Since 2017, we have been representing the Danish company Universal Robots in the Czech Republic and, since last year, also the Danish company MiR. We supply our customers with complex stand-alone devices that they install and program themselves. We also offer programming and integration of robots into the production or assembly line. We are ready to offer the entire workplace "turnkey", which distinguishes us from the local competition. Thanks to the fact that our Montana company has a design and production department, we are ready to provide a complete solution. These are smaller collaborative robots that usually work on a common line with employees. At the same time, they are characterized by a high level of security. Robotization is a trend of the last few years, the interest of customers is considerable. In some areas of production, they pay off because they do the job more accurately, more reliably and faster. Thanks to the simplicity of programming and installation, these smaller robots can be easily moved to another activity according to the client's needs. In addition, we supply various grippers and other components.
What measures or changes in the company required the start of distribution of robots?
For this segment, we set a special sales team whose members had to go through thorough training. We have a service technician and programmer for new installations and modifications. Since this year, we have created a modern robotics training center on our premises. Until the end of 2018, this activity was provided directly by the importer of the brand in Prague, now it is transferred to distributors. In Kosmonos, we will therefore create a classroom and we will invest in demonstration robots so that those interested can try working with them. We believe it will bring us new customers. We have also recently launched a new website where customers can find a complete range of our activities and services. They include a separate page with an offer of Universal Robots and MiR robots.
So you have strong company development behind you and further plans ahead. Are you satisfied with current developments?
I am satisfied, although we still have many big challenges ahead of us. In addition to the mentioned expansion in the company premises, we have to deal with the increase in administration and, due to the increase in the number of employees, we also want to work on improving internal communication, among other things. However, this is an indicator that we are doing better than expected. DREAMland has clear goals: to continue to develop, provide quality services, be faster and even closer to its customers.
Source: http://www.automa.cz/ cz/casopis-clanky/dreamland-grows-and-with-it-expands-and-improves-all-services-2019_03_0_12000/
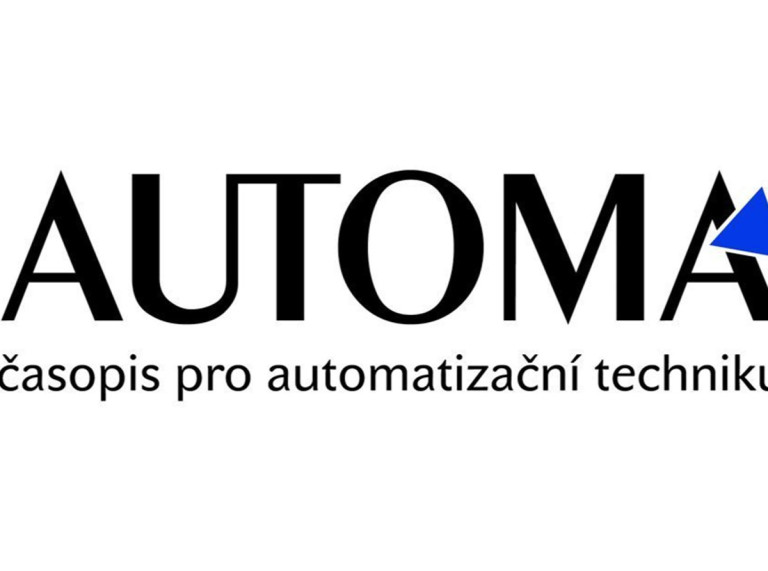